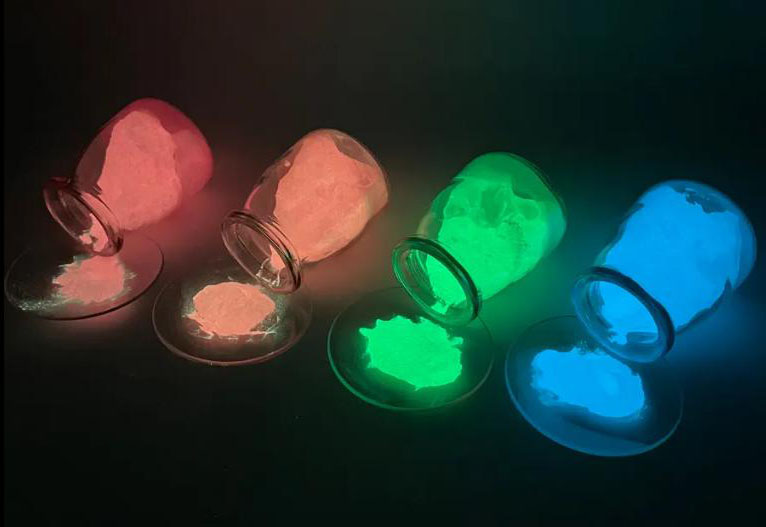
Why Silicon Wafer Quality Matters in Semiconductor Manufacturing?
Introduction
The global semiconductor market continues to grow, driven by advances in technologies like 5G, artificial intelligence, and electric vehicles. According to the World Semiconductor Trade Statistics Organization (WSTS), the market reached $574 billion in 2022, marking a record high (WSTS, 2022). This expansion has increased the demand for silicon wafers, which form the foundation of semiconductor devices.
The quality of silicon wafers is critical in determining the performance, reliability, and efficiency of semiconductor components. Factors such as crystal purity, surface flatness, and dimensional precision are essential for achieving consistent results in processes like lithography, etching, and thin-film deposition.
Key Factors Affecting Silicon Wafer Quality
Crystal Structure and Purity
Monocrystalline silicon with ultra-high purity, often exceeding 99.999999999% (or "nine nines"), is the gold standard for semiconductor manufacturing. Such purity ensures minimal disruptions in electron flow, enhancing the efficiency of devices. However, crystal defects, such as dislocations or grain boundaries, create localized stress fields that impede carrier mobility and increase resistivity.
These defects can also lead to shorter carrier lifetimes, reducing the performance and lifespan of devices. Advanced production methods, such as the Czochralski process, are employed to minimize these imperfections and produce wafers with uniform crystal structures.
Surface Quality
The surface condition of a silicon wafer significantly impacts manufacturing precision. Dust particles, residues, and scratches disrupt the flatness required for photolithography and etching processes, leading to defects in circuit patterns. For example, surface contamination can cause uneven thin-film deposition, resulting in inconsistent device performance.
Polishing and cleaning technologies, including plasma cleaning, are commonly used to enhance surface quality. These techniques remove contaminants and smoothen the wafer, ensuring it meets the stringent standards required for semiconductor fabrication.
Dimensional Accuracy
Precise control over wafer dimensions, including diameter, thickness, and flatness, is crucial for both mechanical stability and processing efficiency. Larger wafers allow manufacturers to produce more chips per batch, improving cost-effectiveness. However, as wafer sizes increase, maintaining uniform thickness becomes challenging. Variations can lead to warping or fractures during processing, impacting yield rates.
Manufacturers employ automated inspection systems to monitor dimensional accuracy and identify potential flaws early in production, ensuring consistency across batches.
How Wafer Quality Impacts Semiconductor Performance
Electrical Properties
The electrical performance of a semiconductor device is directly linked to the quality of the silicon wafer. Impurities and lattice defects disrupt electron mobility, increasing resistivity and reducing efficiency. Even trace amounts of impurities, such as iron or copper, can scatter electrons and degrade the material's conductivity.
In addition, dislocations in the crystal lattice create stress points that lead to power loss and reduced reliability. These issues underscore the importance of maintaining rigorous quality control throughout the wafer production process.
Surface Precision
A smooth and defect-free surface is essential for accurate photolithography and thin-film deposition. Uneven surfaces can distort patterns, affecting the structural integrity of circuits. For example, in the production of multi-layer chips, a lack of surface flatness may cause misalignments between layers, reducing the overall device reliability.
Impurity Control
Impurities in silicon wafers significantly impact resistivity and carrier mobility. Effective impurity control ensures consistent electrical properties, which are critical for achieving high-performance devices. Manufacturers rely on advanced filtration and doping techniques to regulate impurity levels and optimize wafer properties.
Advances in Silicon Wafer Manufacturing
Modern wafer manufacturing has benefited from technological innovations that improve both quality and efficiency. The Czochralski process has evolved to produce larger, high-purity crystals, while advanced cleaning techniques, like reactive plasma treatment, ensure pristine surfaces.
Automated inspection technologies, including defect mapping and electron microscopy, enable early detection of imperfections. These tools allow manufacturers to address issues before they affect the final product, enhancing the reliability of semiconductors.
Conclusion
Silicon wafer quality is fundamental to the success of semiconductor manufacturing, influencing every aspect of device performance and reliability. As demand for advanced technologies grows, maintaining high-quality standards in wafer production becomes increasingly critical.
Stanford Optics supports this effort by offering advanced materials and tailored solutions to meet the stringent requirements of modern semiconductor manufacturing. With a focus on precision and innovation, Stanford Optics enables manufacturers to achieve exceptional results in their pursuit of next-generation technologies.
References: